Tackling the plastic waste problem now mainly involves degradable substitutes or mechanical recycling. However, only high-value wastes such as used shampoo and water bottles, which account for just 16% of plastic wastes, are sorted, cleaned, ground, melted and re-molded into new products. For most plastic wastes, the recycled products are of lower quality and have limited uses.
Ningbo-based startup COMY Energy has developed a chemical recycling process to deal with low-value plastic wastes such as films and takeaway containers that are hard to recycle mechanically. Through a process called anaerobic catalytic pyrolysis, COMY breaks down plastic wastes into their chemical building blocks, namely monomers, which can then be used to make new high-quality plastics.
“The outputs are new virgin-quality plastics that can be used in the food and pharmaceutical industries,” Wei Sikai, COMY’s Marketing Director, told CompassList recently.
To prove the viability of its technology, COMY set up a pilot plant in 2016 in Rizhao in Shandong province. From 2016–2020, the facility operated for over 20,000 hours, demonstrating COMY’s automated processes and solutions to over 160 local and foreign companies, including Sabic, BASF and Dow Chemical. The startup has landed 10 clients, with another 30–40 prospects. Another factory in Dongying, also in Shandong province, is fully licensed and is now being commissioned.
After years of bootstrapping, COMY, which was founded in 2014, raised external funding in 2020 from Petrochemical Haida. “Financing is not a priority for us. Once our Dongying factory is operational, the revenue will be enough to cover all the costs,” said Wei, who declined to disclose the funding amount.
High-value, low waste
COMY’s catalytic pyrolysis process can convert plastic waste into light gasoline and diesel for petrochemical companies to make ethylene, propylene and benzene – all raw materials for making plastics. The company can also make and supply the materials using its proprietary technology.
According to Wei, COMY’s olefin metathesis process – an organic reaction involving hydrocarbons– differs from conventional plastic production technology. "It is about 60% versus 20–30%,” he said, referring to the higher yield of products like ethylene, propylene and benzene.
The outputs are new virgin-quality plastics that can be used in the food and pharmaceutical industries
COMY uses catalysts in its pyrolysis process for higher reaction efficiency. No oxygen and water are needed. The reaction happens at one bar pressure and 350–430˚C, compared to the 600–900˚C required for conventional pyrolysis. “The cost will increase by RMB 100–150 for every 100 degrees increased,” Wei said.
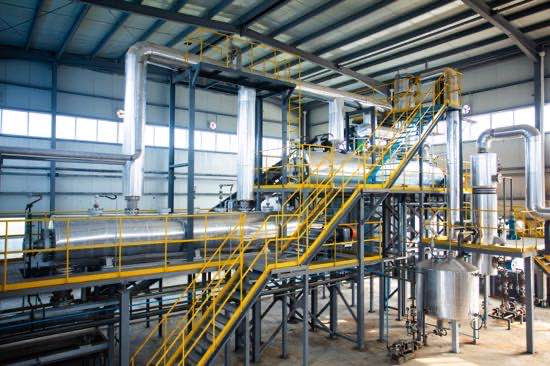
“The odds are in our favor. Millions of catalysts are available, and we found a very good option after only about 1,000 experiments. Some others in this space have spent 10 years on catalysts but ended up with nothing,” Wei said, stressing that COMY’s catalyst contains no heavy metals.
According to Wei, no toxic gases such as dioxin are generated. Carbon emissions are also much lower than the plants that incinerate plastic wastes and conventional petrochemical companies that use oil to produce plastics.
“When included in the carbon trading market, we can sell the credits, which will be another source of revenue,” he said.
Clients at home and overseas
Chemical recycling is capital intensive. According to Wei, building a production line costs 8-digit RMB, but it is economically viable. With COMY’s solution, a ton of low-value plastic waste could generate about RMB 3,000 in revenue. “A factory with a daily capacity of 100 tons can break even in three to five years,” Wei said.
COMY tailors the pyrolysis equipment for clients based on their waste feedstock, scale and the final products they want – light gasoline and diesel or raw materials like ethylene and propylene. “Clients usually buy our equipment, catalysts and technical support. We assist in their operations and help train their personnel,” Wei said.
The company recently signed a contract with a petrochemical giant, but Wei refused to disclose its name. “It wants to invest in our factory in Dongying, which will have an annual capacity of 40,000 tons with six production lines,” Wei said. “We’ve built one line, and the investment will be used to build the remaining five.” Under the contract, the petrochemical company will use all the final products from the factory to make new plastics to be sold to Europe.
A factory with a daily capacity of 100 tons can break even in three to five years
COMY has also secured domestic contracts. It was the only bidder to design a chemical recycling factory with a daily capacity of 120 tons for the Chongqing Environmental Health Group. “We are also very likely to be the only bidder to supply the equipment,” Wei said. The company is also discussing with Qiaoyin, China’s biggest waste management company, the possibility of integrating COMY’s solution into its waste disposal process in some of the 300 cities it operates in.
COMY is also expanding to countries like Japan and New Zealand. "Japan is famous for its garbage sorting, but low-value waste plastics began to pile up as countries like China and others in Southeast Asia said no to [such wastes],” Wei said.
Uphill battles
COMY’s efforts in chemical recycling date back to 2009 when its co-founders set up an R&D lab in Hefei, the capital city of Anhui province. Co-founder Xin Ben’en, a former senior executive at Chinese home appliance maker Midea, teamed up with a scientist whose identity Wei declined to disclose, to solve the plastic pollution problem using petrochemical technology.
It wasn’t an easy journey. Regulations made in 2007 by the State Environmental Protection Administration (now the Ministry of Ecology and Environment) prohibited plastic wastes from being used for oil refining. “Such a rule amounted to a no to all work on chemical recycling in China,” Wei said. “We explained to the government that the rule was due to concerns over environmental pollution, but we would not generate any pollution.
“When we applied for approvals from multiple authorities to build our first factory, we were told that there was no such category called chemical recycling. Finally, they decided to apply the most strict standards on us, treating us as a petrochemical company,” Wei said.
According to Wei, the situation is improving. Last June, the China Petroleum and Chemical Industry Federation set up a chemical recycling task force with Sabic, BASF and Dow as its members. In April this year, the Ministry of Ecology and Environment issued a directive that encourages chemical regeneration.
“Although using a different term – the ministry refers to converting waste plastics into buffer – it is oil or monomers that can be used to make new plastics,” Wei said. “It may not be state-level support, but at least you are allowed to do it. We are expecting to see more specific policies to support the industry.”
CORRECTION: An earlier version of this article misstated that COMY has applied for a license to operate the factory in Dongying. The company has since clarified the factory is fully licensed and is being commissioned. COMY also previously said that conventional pyrolysis happens at 1,400°C and the cost of pyrolysis increases by RMB 100–150 for every one degree increased. It has since clarified that conventional pyrolysis happens at between 600°C and 900°C and the cost of pyrolysis increases by RMB 100–150 for every 100°C increased.