Barcelona-based startup Oimo has developed a seaweed and algae-based bioplastic composition compatible with existing plastic injection molds, allowing traditional plastic manufacturers to make fully biodegradable plastics that can be decomposed in less than a month.
Founded in early 2019, Oimo – which stands for Organic, Intelligent, Malleable Objects – currently offers bioplastic ring can holders for four or six-pack beverages and a near-transparent film used in food packaging.
“Our material is aimed at replacing single-use plastic applications," Albert Marfà, CEO and co-founder of Oimo, said in an interview in August. "All the materials we have come up with are biodegradable either in salt- or freshwater, or with heat; and we have managed to make them biodegrade in less than a month in seawater, which not many [biomaterials] can achieve.”
The global bioplastics is growing rapidly, driven by increasing consumer concern about the environmental damage caused by conventional plastic and the urgent need for more environmentally friendly substitutes. The market is forecast to reach $19.93bn by 2026, from $6.04bn in 2018, according to Fortune Business Insights.
The EU alone has committed to banning single-use plastics from 2021, which means plastics manufacturers will soon need to switch to solutions thatallow them to maintain their production levels with existing machinery.
This, Marfà said, would be Oimo’s chance to scale. The startup will look at raising €1m seed investment to fund such growth, including expanding its team from the current four full-time staff and its small lab facility.
Common plastics can take hundreds of years to degrade. They also release harmful toxins when burnt, and even contaminate the food chain. Eight million metric tons of plastic waste enter the world's oceans annually on top of the estimated 15m metric tons already in the marine environment, posing a major threat to marine life and can kill animals as large as whales. Without urgent intervention, 1.3bn tons of plastic will end up in the natural environment by 2040.
Early days in London
Marfà, who’s from Barcelona, created his bioplastics startup in 2017 during his undergraduate studies in industrial and product design at London's Brunel University. “My inspiration came from being by the sea in Barcelona and seeing more and more plastics end up in the ocean. So I wanted to tackle that problem by focusing on the long time that plastics take to degrade in the ocean and how they harm marine life,” he said.
Although he had no experience in biotechnology, Marfà read books andwatched online tutorials on the subject and received advice from university tutors.
“For my final university project, I had the chance to work with many experts in the area of plastics and had access to machinery and tools at the university that really helped me to develop a formulation that mimicked plastic," he said. "Looking into bioplastics and just doing my own formulations we managed to come up with one that could mimic ring can holders for beverages and this was the first product.”
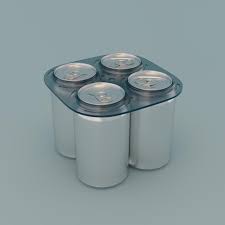
Marfà did not fully realize the significance of his discovery at the time but others did. Using a cash award from a business competition at Brunel, he set up a company to promote his university project, naming it Edible Plastic, after the material's organic nature.
In early 2019, Marfà added fellow Brunel student, friend and business management and marketing graduate, Clara Hardy, as a co-founder. They renamed the company Oimo and relocated to Spain after receiving €150,000 in pre-seed funding from a local family-run business. An innovation grant of €75,000 from the Catalonian government followed.
Targets 2021 commercial launch
Oimo’s bioplastics are entirely made from organic matter, including seaweed and algae. But the source materials, said Marfà, could also be “leaves, extracts of oils or even waste.” Seaweed is favored because it is vegan and, unlike some organic waste, potentially attractive to clients. Besides, seaweed can be sourced in large quantities from Spain’s Atlantic coast.
“We make the material in a compounding process where it is mixed with other ingredients like natural sugars and vegetable oils and heat them to a high temperature, just below that used for polypropylene plastic, to produce a chemical reaction. This allows them to obtain a series of molecular chains that adhere to create the bioplastic, mimicking the mechanical properties of normal plastic,” Marfà said.
The material is then extruded and can then be heated again and remolded. The strength of the material produced can vary according to both the raw material and the heat. For example, different seaweeds have different properties and there are therefore multiple compositions possible.
The company has applied for one EU-wide patent and will consider more patents for its different compositions. The startup is currently in the Spanish and Chinese markets, as well as developing leads in France, Germany and the US.
Easily and locally available raw materials are preferred. If Oimo secured a customer producing organic waste, for example, Oimo would try to use the organic waste as the main material for its bioplastic. This reduces costs, and lowers CO2 emissions as materials no longer need to be transported between sites.
Biodegrades in natural environment
Oimo chose not to produce the material itself. Its business model is to license the use of Oimo's composition, with the final bioplastic product and price varying according to the needs, sector and size of the organization. To encourage take-up, the startup plans to offer its products for free trials and testing.
“We are formulators so we adapt our plastic to each requirement because certain clients will want certain materials to be used or one set of properties for that plastic,” Marfà said.
”The advantage of us not producing the material ourselves and being able to contract that out means that we can localize the value chain, keeping the raw materials, the compounding process and manufacturing in the same market, reducing C02 emissions significantly.”
Oimo’s bioplastics cost about €2.50 a kg to produce, which is similar to PLA bioplastic, but, according to Marfà, price can never be the only consideration in switching to bioplastics because, unless the economies of scale change, bioplastics can “never be as cheap as conventional plastic," costing from $0.50 per kg.
Oimo's greatest advantage over other bioplastics is its rapid and complete biodegradation in the natural environment. “The only common bioplastic we had in the past, PLA [polylactic acid], had a mixed reputation because it is only compostable in industrial plants,” Marfà said.
“Thismeans that, if it ends up in the environment, it won't biodegrade. It needs to be collected and sent back to a different site, taking time, money and creating emissions and I believe this is the reason the bioplastics market was not growing.”
Strong Chinese interest
Oimo may be an answer to the imperfect PLA bioplastic but can they compete with the gigantic traditional plastics industry? According to Marfà, the industryis willing to engage, including companies in China, the world's largest plastics producer, because the Chinese government is eager to move away from the use of traditional plastics.
“We have had positive feedback from the plastics sector [in general]. They are willing to try new technology even if it comes from a small startup," Marfà said. "The sector'strade events are focusing on sustainability and if you go to them with a solution, they will listen to you and even lend you their machinery to try it out.”
In 2019, Oimo won the New Material Award at Guangzhou's Institution of Engineering and Technology, and participated in the Shanghai-based accelerator, Xiji. Oimo has a team of three freelancers in China attending trade events and paving the way for commercialization, looking for both suppliers and manufacturers.
“The Chinese government is setting many laws in that area and was going to try to go plastic-free in Hainan province from January this year but that stalled due to Covid-19,” Marfà said.
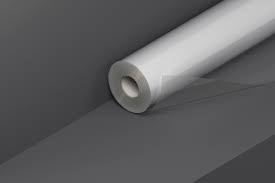
Pellets ready and waiting
The most significant development for Oimo's scalability is the successful development of its first pellet two months ago. These small granules, which are the basic ingredients to make plastics, are heated and ground in either an injection mold or an extruder and are then made into different shapes.
“All traditional plastic materials are sold in pellets that feed into the machines. If you don't have a pellet, you can't supply to any manufacturer,” Marfà said. "If new materials are not in pellet form that can be melted and remolded, they won't be able to make an impact and manufacturers would need to change their machinery, which is unlikely to happen.”
The company, said Marfà, looks at the mechanical properties of plastics and tries to replicate them with its material. “Oimo mimics two types of plastics used in the market. LDPE [low-density polyethylene] which is the plastic used for flexible films for packaging and HDP [high-density polyethylene] or PP [polypropylene], which are the rigid plastics in food containers, caps and straws.”
Its bioplastic that mimics plastic bags could hold 10–20kg in weight, based on tests conducted by the company. To date, the company has conducted pilots at two private Spanish plastic institutes.
“They were quite surprised the material could extrude like it did and that it biodegrades so quickly when it reaches seawater,” Marfà said.
Oimo is looking to trial the pellets in a large company and is about to send product samples into the marketplace. Oimo won’t be manufacturing the pellets itself but will contract it out to any company with adequate capacity to supply to clients. The product is receiving “a lot of interest from the food and beverage industry and also agriculture and cosmetics,” Marfà said.
Oimo considers itself a pioneer in its field in Spain. “Besides there not being many competitors, they haven't adapted their business model in the same way we have. They have their own manufacturing plant and make the pellets themselves, so they have limitations in supply and the price is really high,” Marfà said.