In 2012, Carlos Casanovas was studying for his master’s in mechanical engineering at the Massachusetts Institute of Technology (MIT) when, while researching floating wind turbines, he conceived an idea that later became PivotBuoy, an innovative single point mooring system for floating offshore wind turbines.
Offshore wind turbine platforms are not new, but, according to X1 Wind, the startup Casanovas co-founded, its PivotBuoy floating system design enables “dramatic” reduction in platform weight by up to 80%, compared with more commonly used semi-submersible and spar buoy structures. The wind power tapped in a single installation could reach up to 50MW, enough to power about 12,000 homes in Spain.
This means X1 Wind’s model is lighter, easier to install and, most importantly, more economically feasible. Once launched, it will help pave the way for more floating offshore wind turbines that Europe needs in order to meet its target of offshore wind delivering 25% of its electricity by 2050, as part of its goal to be carbon neutral by then. To get there, Europe needs 150 GW of floating wind turbines by 2050, from 62 MW it currently has.
“Over the last decade, a number of prototypes have successfully proven floating wind is technically feasible, but costs need to be reduced by at least 50%,” said CEO Alex Raventos, who, together with Casanovas, the current CTO, founded X1 Wind in 2017.
A 2018 US Department of Energy report cited a similar demand for “accelerated cost reductions” in the offshore wind turbine industry. Addressing this, X1 Wind’s PivotBuoy solution aims to significantly lower manufacturing, deployment and maintenance costs of floating wind turbine platforms compared with current market solutions. That means getting its Levelized Cost Of Energy (LCOE) down to €50/MWh, which will give it a significant lead in a market where prices range between $74/MWh and $79/MWh. LCOE is a measure of the average net present cost of electricity generation over the lifetime of a plant.
The EU has committed to spend at least €1tn under its Green Deal Investment Plan to become carbon neutral by 2050. X1 Wind, which has already model tested PivotBuoy at 1:64 and 1:50 scales, received €4m in April 2019 from the EU’s Horizon 2020 research and innovation program to demonstrate its LCOE for floating wind turbines could fall by as much as 50% using PivotBuoy.
Unlocking downwind potential
The PivotBuoy uses a modular design comprising a lower body and an upper body. The lower body is moored to an anchor using a mini-TLP (tension leg) mooring system. The electric cable is also connected to and hangs off this lower body. The upper body, which holds the floating platform, is joined to the lower body at a single, quick connection point.
The ability to easily disconnect the upper body from the lower body means the floating platform can be towed easily to port or sheltered waters for maintenance. The modular design also means that the structure can be assembled onshore and transported to the offshore site for installation, all of which potentially reduces operations and maintenance costs. The floating design also enables deployment in deeper waters further offshore to take advantage of stronger winds.
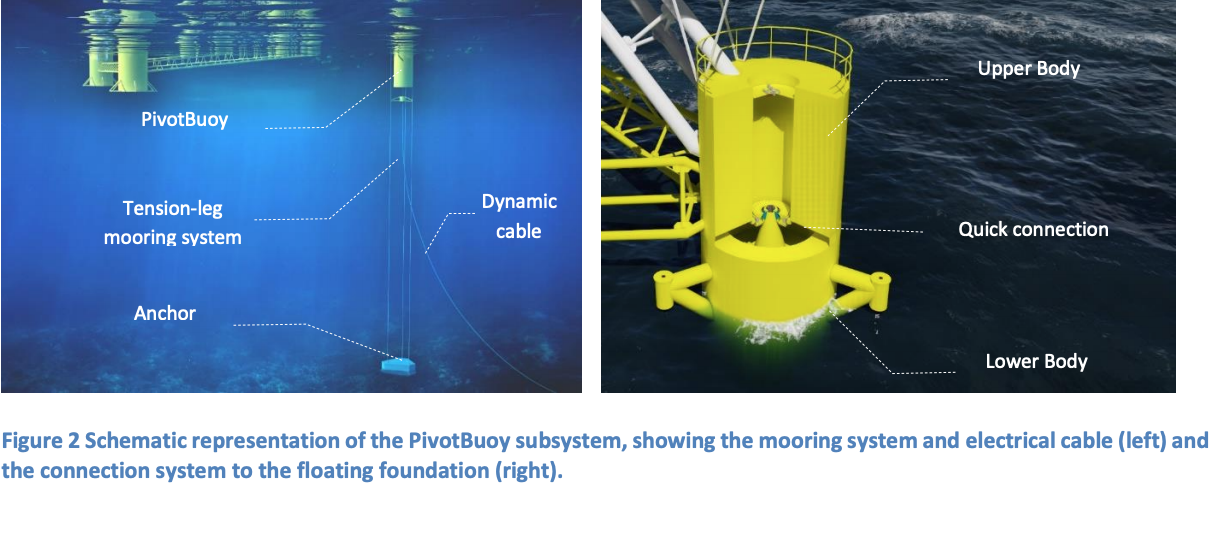
The upper body’s ability to pivot freely allows the whole structure to weather-vane and orientate passively in the direction of the wind, which means that downwind turbines can be deployed easily and with less cost without the need for a large tower, ballast mechanisms for stability and yaw actuators to turn the turbine towards the wind, all of which are needed in traditional upwind turbines.
According to X1 Wind, its PivotBuoy platform, which enables the switch from upwind to downwind configuration, unlocks the potential of lighter and more flexible wind turbine designs. This, it said, is necessary to scale to large downwind blades up to 200 meters long that could, in future, power up to 50MW. By avoiding the need for a large tower the PivotBuoy design also minimizes the “tower shadow” drawback associated with downwind designs.
Santiago Canedo, a mechanical engineer with over 18 years’ experience in wind turbine design, led the X1 Wind mechanical team that converted an upwind Vestas V29 225kW into a downwind configuration for testing with the PivotBuoy system this year.
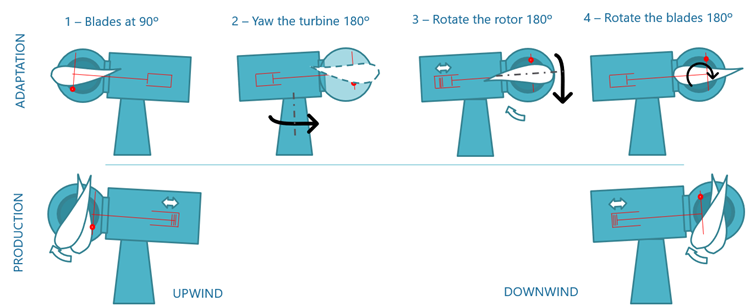
Banking on synergies
X1 Wind received its initial funding in 2018 from EIT InnoEnergy, under the EU’s Horizon 2020 program. This was followed by a further €4m under the same program.
“During the last decade, it has been demonstrated that speeding up the commercialization of offshore wind technologies process means driving down costs and contributing to European competitiveness,” PivotBuoy said in a document on its techno-economic model published online.
“The European Union is increasing the funding for research and innovation in floating offshore wind focused on cost-competitiveness, where PivotBuoy is an example.”
The global offshore wind energy market size surpassed $24bn in 2019 and is forecast to exceed $75bn by 2026, based on a CAGR of 14.8% that’s driven by favorable regulatory policy, especially in Europe, Global Market Insights said in a research report. “Respective governments and market players are investing aggressively toward clean energy sources," it said.
X1 Wind’s EU-funded project to test PivotBuoy runs from April 2019 to March 2022, with the participation of a consortium of eight members from five countries with expertise in the oil and gas, naval and energy sectors. This reflects the wide applicability of the PivotBuoy design in the wind and wave energy, and oil and gas industries.
The R&D and industry partners include EDP, IntecSea of Worley Group, PivotBuoy’s manufacturer DEGIMA, and the PLOCAN test site off the Canary Islands, where the PivotBuoy design is being installed for final testing. Each member has a role in the project based on its expertise. This includes design, manufacturing, assembly, installation and testing, performance and risk assessments as well as cost and social impact assessments.
In March 2020 the company revealed details of its PivotBuoy design and the beginning of its manufacturing phase at DEGIMA’s facilities in Santander. The company targeted 2020 as the year for the official launch, installation and technology validation, and is slightly behind schedule.
“One of the main challenges has been to maintain the manufacturing schedule during the Covid-19 pandemic. Within the project, we have worked with suppliers from all over the world, making the coordination a challenge,” said Casanovas.